Digital transformation is revolutionizing CNC machining shops, enabling them to optimize processes, improve accuracy and offer more efficient solutions to their customers. Integrating emerging technologies is essential to stay competitive in a constantly evolving market.
In this article, we will explore how digitization impacts CNC machining shops and the key strategies for successful implementation.
Benefits of digitization in CNC machining shops
The adoption of digital technologies in CNC machining shops offers multiple advantages that improve efficiency and quality of services:
- Process optimization: Digitalization allows for more efficient management of operations, reducing production times and minimizing human errors.
- Improved accuracy: CNC machines integrated with advanced digital systems ensure greater accuracy in machining parts, meeting tight tolerances and specific customer requirements.
- Efficiency in project management: Digital tools facilitate the planning and monitoring of projects, ensuring compliance with deadlines and optimizing the allocation of resources.
- Adaptability and customization: Digital technology enables workshops to adapt quickly to changing market needs, offering customized and flexible solutions.
Emerging technologies in CNC machining
CNC machining is evolving through the adoption of emerging technologies that optimize production and improve accuracy. Artificial intelligence, for example, makes it possible to improve machine programming, automate cutting paths and detect patterns in production data. This facilitates real-time adjustment of machining parameters, reducing waste and improving the quality of manufactured parts.
Another significant advance is additive manufacturing, which complements CNC machining processes by enabling the rapid creation of prototypes and complex parts that would be difficult to manufacture using traditional methods. This combination offers greater design flexibility and reduces validation costs prior to mass production.
Automation is also gaining prominence with the incorporation of collaborative robots, which facilitate the loading and unloading of parts, minimizing human error and optimizing production time. Added to this is the use of digital twins, virtual models of machines or processes that allow operations to be simulated before physically executing them, which improves planning and reduces maintenance costs.
Finally, the Industrial Internet of Things (IIoT) connects CNC machines with management systems through sensors, allowing real-time data collection for predictive maintenance and optimizing equipment performance.
The integration of these technologies not only increases productivity, but also ensures greater control over quality and delivery times, key aspects for competitiveness in the CNC machining industry.
Strategies for successful implementation
For CNC machining shops to effectively integrate these technologies, it is recommended:
- Assess specific needs: Identify areas that would benefit most from digitization, such as machine programming, project management or quality control.
- Select appropriate tools: Opt for technological solutions that are aligned with the workshop’s objectives and are compatible with existing systems.
- Train staff: Invest in employee training to ensure effective adoption of new technologies and minimize resistance to change.
- Monitor and adjust: Continually evaluate the performance of implemented technologies and make adjustments as needed to optimize results.
I-MAS: Innovation and digitalization in CNC machining
With more than 20 years of experience in the sector, i-mas is committed to digitalization as a key strategy to improve our efficiency and competitiveness. The integration of artificial intelligence and automation in our processes has allowed us to optimize the programming of our CNC machines, reduce production times and ensure maximum precision in each manufactured part.
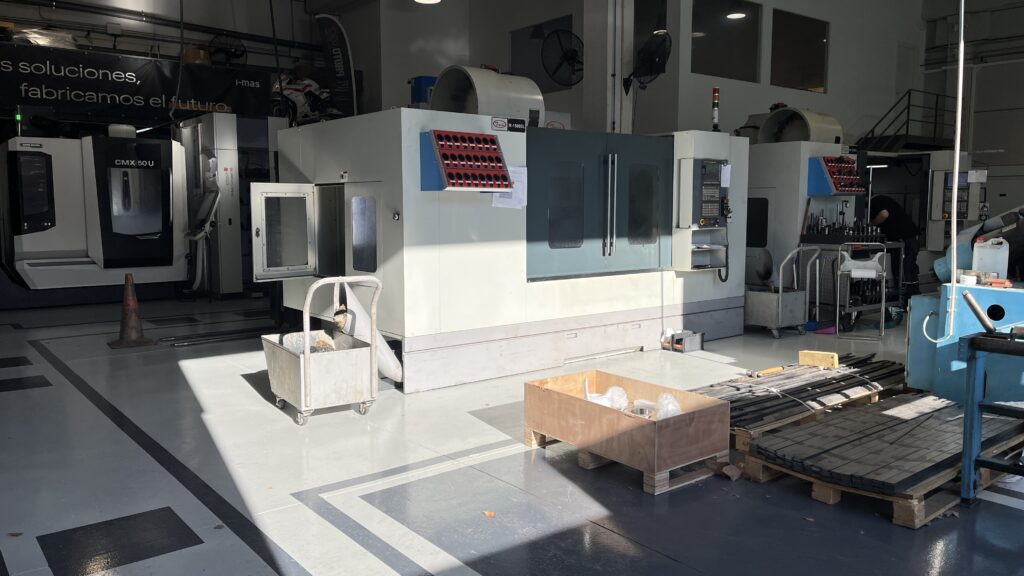
i-mas Machining Workshop
Thanks to these innovations, we have been able to improve our operational capabilities and respond more quickly to market needs. We continue to evolve and adopt new technologies to remain at the forefront of CNC machining and offer advanced solutions to our customers.
If you have a project in mind or are looking to optimize your production processes, do not hesitate to contact us.